Human-robot collaboration in the manufacture of axle transmissions The worker with seven axes While not too long ago operators at the BMW Group plant in Dingol昀椀ng had to lift and 昀椀t di昀昀erential cases for front-axle transmissions in the tightest of spaces, the early adaptation to Industrie 4.0 has now radically changed the workplace. A specially designed human-robot collaboration (HRC) solution from 阀阀 Systems is now relieving the sta昀昀 of all strenuous tasks while making the plant future-proof at the same time. Lifting 5.5 kg differential cases that are The robot fits seamlessly into the pro- �This highly effective KUKA solution is difficult to grip, and fitting them with duction environment. Not a single forward-looking Industrie 4.0 technology millimeter accuracy in the tightest of adjustment of the production line was at its best – individually adapted to spaces – thankfully, this back-breaking necessary for installation. The biggest the conditions of a production line, intel- task is now a thing of the past for the benefit of the new automation solution ligently networked with the control operators at the BMW plant in Dingolfing. from KUKA is that the human colleagues systems, space-saving, and designed for Today, this immensely arduous work of the LBR iiwa robot can safely move close collaboration with the machine step is handled by an LBR iiwa light- about in the production zone. For this operators. In short: the production of weight robot with utmost precision and purpose, the robot gripper is equipped the future is already underway at efficiency. with an HRC case, so that the operator the BMW Group plant in Dingolfing. is protected from injury at all times. To maximize the LBR iiwa’s efficiency, And this is what the collaboration KUKA has developed a slim steel structure, between humans and robots looks like: which is mounted on the ceiling. From the processed components are auto- an overhead position (and thus saving matically transported to the system via space), the powerful yet sensitive ma- a conveyor and are prepared by the chine goes to work. The entire control operator. The operator places all of the technology including the interfaces for small and lightweight parts, such as the system controller has also been spacers and ball bearings, into the trans- accommodated in the available space. mission case and the cover. The worker then activates the robot, which fits the heavy differential case in place. Next, the operator fastens the cover to the trans- mission. The procedure takes no more than 30 seconds. Human operators and robots collaborate to install di昀昀erential cases for front-axle transmissions. 88�89
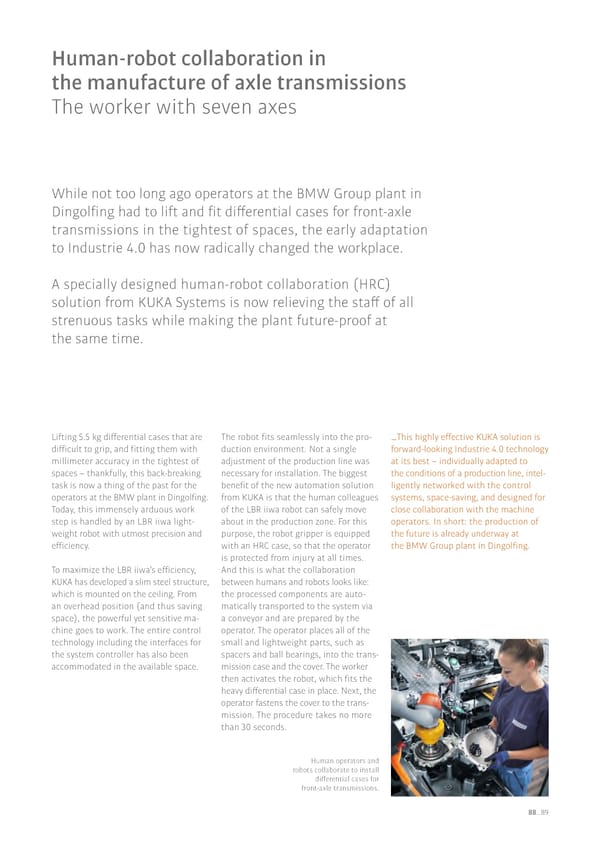