Logistics �Now. Everything. Always. Customized products and same-day delivery – customers have a growing expectation that everything will be available in all places, at all times. This ubiquity places the utmost demands on the logistics and process chains and is increasingly embra- cing the stationary retail sector and the structure of merchandise 昀氀ows. The boundaries between individual delivery channels are successively vanishing and modern distribution centers are often being set up directly in metropolitan areas thanks to the reduced space requirements. Changes that can only be addressed through highly transparent, digitized networking of production and logistics. In this context, 阀阀 sees itself as a solution provider translating the individual requirements of the market participants into 昀氀exible, networked and software-supported logistics concepts. M2M Communication �The universal communicator. Machine-to-machine communication, or M2M, is the automatic exchange of information between machines. These may be vastly di昀昀erent Protocol end devices, from production machines through vending machines to vehicles or household appliances. A standardized set of rules is needed for M2M communication to work – in modern terms: a protocol. Such a standardized software interface enables universal communication. The most promising protocol at this time is the Open Platform Communications Uni昀椀ed Architecture (OPC UA). Machine Learning �Knowledge through experience. Intelligent machines garner their knowledge through experience. In the case of networked machines, it is irrelevant whether the experience is their own or originates from swarm intelligence. An artificial system always learns by comparing the desired objective and any anomalies that occur. It can recognize correlations, patterns and general rules, draw conclusions from them and modify its future behavior, this synthetic process being referred to as machine learning. Especially in unstructured environments and with highly flexible processes like Industrie 4.0, machine learning in a swarm or in the cloud is an effective method of adapting production processes intelligently and autonomously to the individual framework practically in real time. Manufacturing �Access rather than ownership. Digitization has substantially changed the approach to physical possession. This is increasingly being replaced by temporary access to goods or as a Service (MaaS)/ services. The best example: music streaming. What has already become an everyday situ- ation in many consumer segments will also revolutionize the industrial environment over Robotics as a Service the next few years. As the name implies, manufacturing processes are provided as a service when offering “Manufacturing as a Service”: the machine does not change ownership, and ® only the service of the machine is paid for (for example in the form of a cost-per-uptime (RaaS) model). What applies to complete production systems will, in the future, also hold true for individual elements within a manufacturing facility – for robots, for example. On the basis of a “pay-per-use” model, it will not be the physical object itself that is purchased in ® conjunction with “Robotics as a Service ”, but rather its performance, such as weld spots in vehicle body production, for instance. The smart factory of the future integrates these services seamlessly into its production processes and thus has the capability of reacting to varying capacity requirements and goods flows exceedingly flexibly and efficiently while conserving resources at the same time. Ultimately, these business models uproot traditional ideas of what a value chain may look like: the principle of shared production will become more important, allowing the end user to act as a co-producer. If desired, KUKA Consulting analyzes the business models of companies to determine whether they can be marketed profitably as a service (“Product as a Service”). Manufacturing �Expertise is the raw material for creating value efficiently. If the best available expertise can be focused upon every single process step and every single level of activity, all parties Ecosystem involved benefit: product designers, developers, manufacturers, logistics specialists and end customers. A complex network that optimally brings together all relevant expertise in terms of personnel, economy and technology is considered an ecosystem. This comprises hardware and software resources, process and project know-how, consulting expertise and complex networked architectures of production and information technology. What is important for such an interdisciplinary system is that the combined expertise is not just limited to a single company, but that the best possible personnel and the best available knowledge on the market is brought together under one project umbrella. As an experienced player across industries, products and processes at the interface of OT and IT, KUKA is in a unique position to “fuse in” the ideal experts and expertise for any given project. This yields an unbeatable team of resources provided by the customer, KUKA and external partners, with superior know-how and advanced technology from the shop floor to the business model level. Ecosystems add value beyond just optimizing the value creation processes: this bundled creativity allows for new products, solutions and business models to be developed jointly. VI�VII
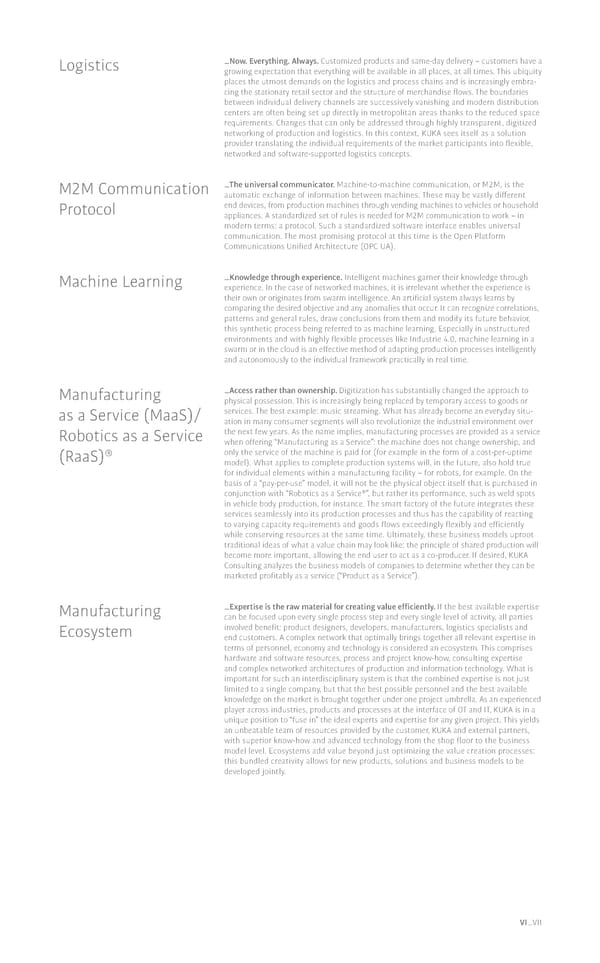