Megatrends �What makes the world go round. Customization, digitization, responsible use of natural resources and demographic changes are the megatrends that will need to be mastered in the coming decades. With a forecast world population of eight billion by the year 2025 and ten billion by 2060, ever more customer requirements of increasing diversity will need to be satisfied. At the same time, demographic changes will be confronting industrialized and emerging countries with economic and social challenges over the long term. Humanity is thus facing a fundamental paradigm shift which will undoubtedly have far-reaching conse- quences for our worldwide economic systems. That is why Industrie 4.0 does not describe a purely technical innovation scenario but rather a way in which intelligent technology can help to overcome the global challenges of the 21st century. As a thought leader and trailblazer for Industrie 4.0, KUKA is working on production environments that increase economic efficiency while also using resources responsibly, which make high-quality goods more affordable and are instrumental in sustainably improving human working conditions in factories. Mobility �Robots on the advance. The production of the future requires greater flexibility – for both faster manufacturing and customized products. One indispensable prerequisite for creating a higher degree of flexibility in industrial environments is greater mobility. This can be achieved by means of episodic, periodic or permanent mobility concepts that each bring about acceleration in industrial production in their own specific ways. For this reason, KUKA is paving the way for this key technology with platforms that can move intelligently and autonomously in order to transport things or machine workpieces. They can find their own way if necessary, aligning themselves with workpieces to within a millimeter or even moving the robot to them. They are also capable of responding autonomously and adaptively to changing conditions in complex logistics and production chains. Mobile auto- mation solutions from KUKA show today what the future holds in store for highly flexible production in Industrie 4.0. Monitoring & �Data in real time. Monitoring and stream analytics compare and analyze data that is available to the smart factory from diverse sources – devices, sensors, infrastructure, etc. Stream Analytics/ In real time they make comparisons with data records from the past, recognize anomalies and are able to categorize faults with the aid of machine learning. On this basis, intelligent Micro Services systems initiate immediate countermeasures and generate forecasts and recommended actions for the future. On-Premises �Software on board. On-premises solutions rely on the infrastructure of the company’s in-house IT. The deployment model of such software can be designed as a service and thus take on the function of a “local cloud”. People First �Production and products for people. In the factory of the future, the focus of thought and action will shift to the human worker with his changed requirements, desires and capabilities. Networked and flexible production technologies combine the cost advantages of mass production with the customization potential of craft manufacturing. This means that the customers’ desire for high-quality individualized products does not lead to higher prices, as is currently the case. But humans are at the center of the future world of goods not only in their role as customers. Intelligent robots that collaborate with humans, and mobile assistance systems will improve the world of work in many different ways. They handle heavy loads, carry out activities that are not ergonomic or are simply too dangerous for people and perform tasks which require levels of precision and speed of which humans are not capable or which are cognitively stressful. Predictive �Eliminating static maintenance intervals. Dependable production planning and maximum machine availability through the avoidance of unscheduled downtime are the practical Maintenance advantages of what is internationally known as predictive maintenance. On the basis of real-time data, all relevant parameters of the machines involved in the manufacturing process are acquired and evaluated for anomalies by means of stream analytics. In a subsequent machine learning process, speci昀椀c fault patterns and the causes of a problem are detected in good time. This results in fewer rejects and maximum availability over the entire life cycle of the production line. The requirements on machine operating times vary depending on the speci昀椀c branch of industry and its product cycles. While this could be up to 30 years in the aerospace sector, it is a matter of just a few months in the case of fast-moving goods, such as smartphones. With the aim of enabling an accurate assessment of the future performance of the machine or one of its components, intelligent predictive maintenance systems interconnect the largest possible amount of data from decentralized sources for the purpose of analysis. Hello Industrie 4.0�Glossary
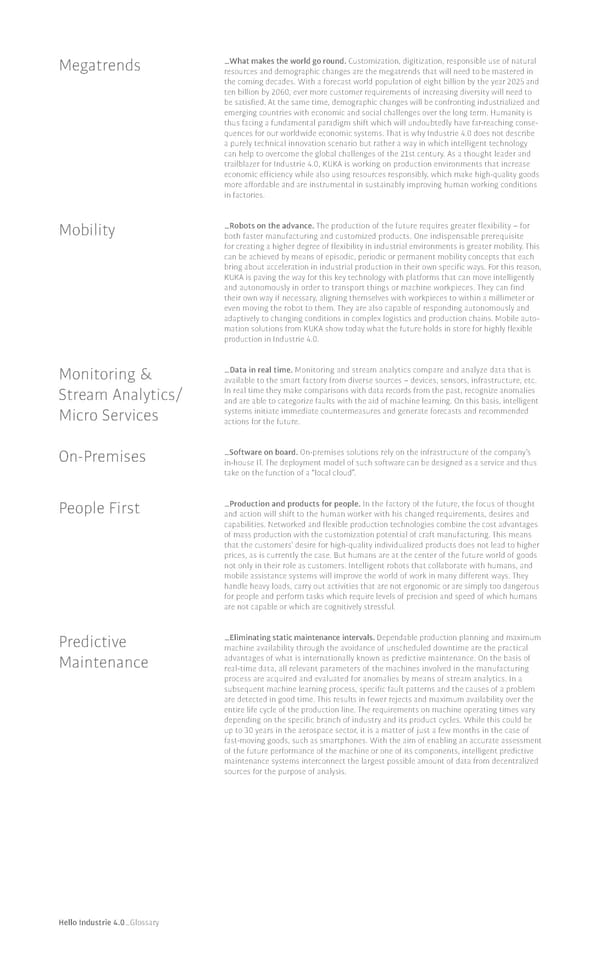